Meta Description: Engineer-proven solutions to combat bolt loosening. Explore mechanical locking nuts, friction-based systems, DIN/ISO standards, and vibration-resistant fasteners for critical applications.
Introduction: The $20 Billion Vibration Problem
Every year, vibration-induced fastener failure costs industries over $20 billion in downtime and accidents. From collapsing bridges to aerospace disasters, loose bolts remain a silent threat. This guide dissects 9 proven anti-loosening technologies backed by ISO/DIN standards, helping you select failsafe solutions for your projects.
(Image suggestion: Split-screen showing vibrating machinery vs. catastrophic bolt failure)
1. Mechanical Locking Fasteners: Positive Engagement
*(Keywords: mechanical locking fasteners, positive locking, DIN 985, ISO 7040, all-metal lock nut)*
How They Work
These fasteners physically interlock threads or integrate deformable elements to resist rotation. Ideal for extreme vibration environments (>15g acceleration).
A. Nylon Insert Lock Nuts
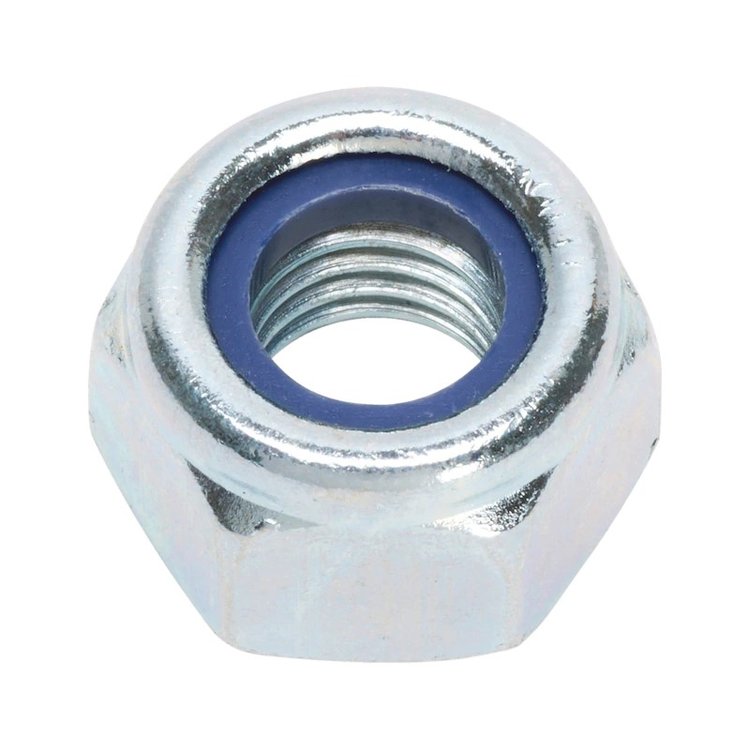
- ISO 7040 / DIN 985: Mandates nylon height ≥50% of thread pitch
- Temperature limit: -40°C to +120°C (Avoid chemical exposure)
- Pro Tip: Specify flame-retardant PA66 nylon per ISO 4589-2 for automotive
B. All-Metal Lock Nuts
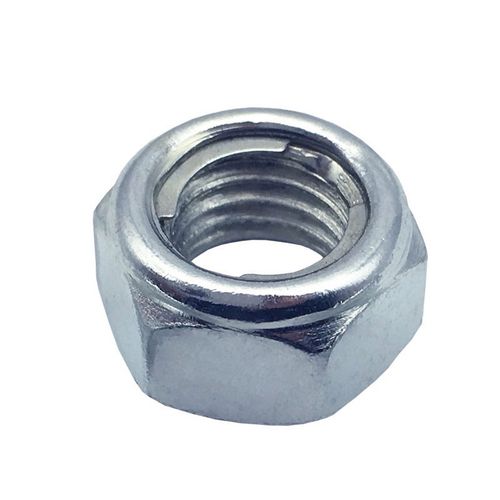
- ISO 2320 Prevailing Torque Nuts:
- Must withstand 100,000+ cycles on Junker vibration test (DIN 65151)
- Reusability: ≤40% torque drop after 5 installations
- Aerospace variant: MS21250 self-locking nuts
C. Castle Nuts + Cotter Pins
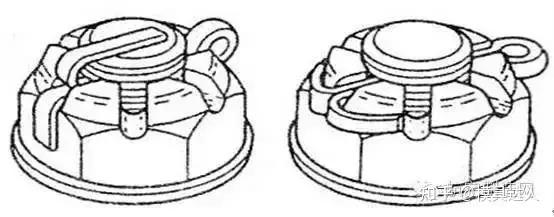
- ISO 7038 / DIN 935 (Nuts) + ISO 1234 (Pins):
- Slot width = Pin Ø + 0.1mm tolerance
- Pin protrusion: ≥1.5x pin diameter
- Critical for wind turbine blade bearings (IEC 61400-22 certified)
2. Friction-Based Locking: Torque Amplification
(Keywords: friction locking fasteners, prevailing torque, jam nut, DIN 6926)
A. Double Nut System
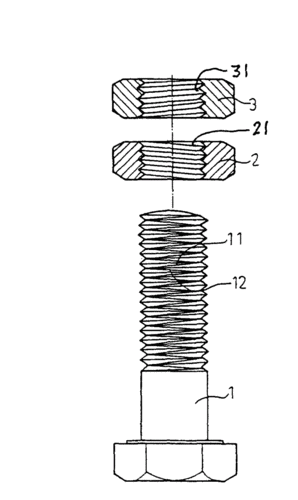
- ISO 4032 (Primary) + ISO 8673 (Jam Nut):
- Jam nut thickness: ≤0.8 x thread pitch
- Torque sequence: Tighten primary to 100%, jam nut to 120-150%
- Caution: Avoid on cyclic thermal expansion joints (>80°C ΔT)
B. Serrated Flange Nuts/Bolts
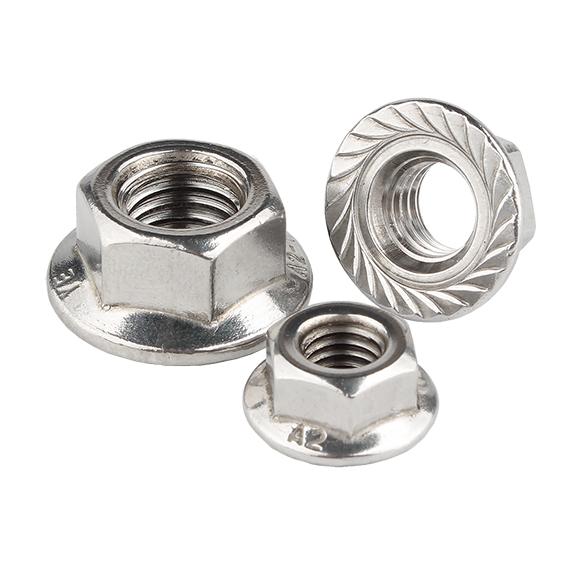
- DIN 6926 / ISO 4161:
- Serration hardness: ≥450 HV
- Minimum bite depth: 0.1mm on steel substrates
- Dominates European automotive chassis (VW TL 52046 standard)
3. Elastic Element Locking: Spring Force Solutions
(Keywords: locking washers, spring washers, DIN 6797, vibration resistant washers)
A. Tooth Lock Washers
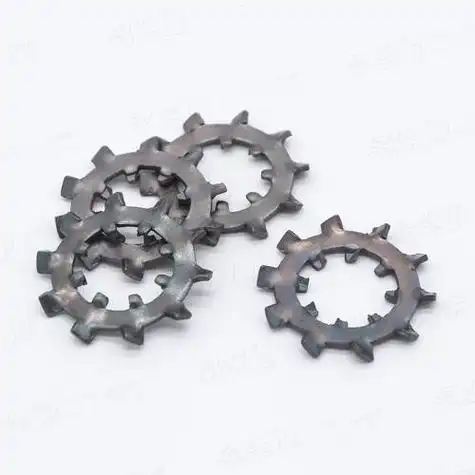
- DIN 6797 Jaws® Washers:
- Tooth hardness: 500-750 HV
- Load capacity: ≥50% of bolt preload (e.g., 8.8 Grade)
- Critical Update: ISO 898-7 now deprecates spring washers for critical joints
B. Belleville Spring Washers
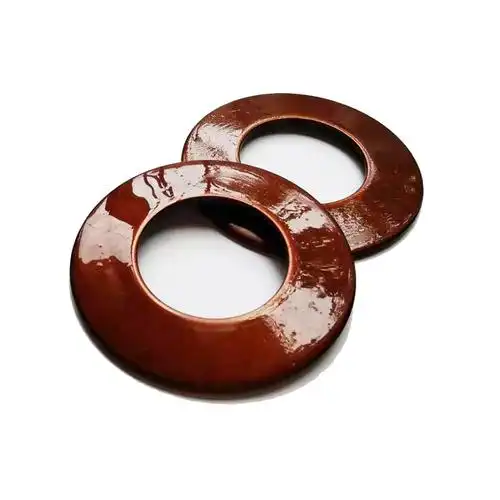
- DIN 6796 / ISO 10688:
- Deflection tolerance: ±10% at 75% load height
- Used in nuclear valve stems (ASME B16.34 compliant)
4. Thread-Form Locking: Geometric Innovation
(Keywords: self-locking threads, Spiralock, wedge locking technology)
A. Spiralock® Nuts
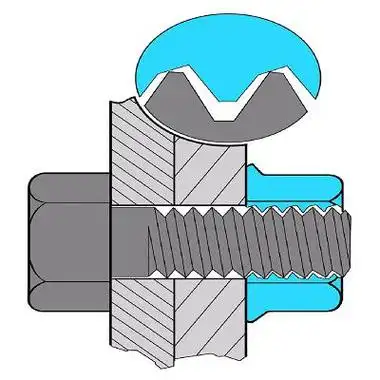
- SAE J995 / MIL-DTL-45938:
- Vibration resistance: 2,000+ hrs (NASM 1312-7)
- Temperature range: -253°C to +650°C
- Case Study: SpaceX Falcon 9 engine mounts
B. Dardelet® Opposing Threads
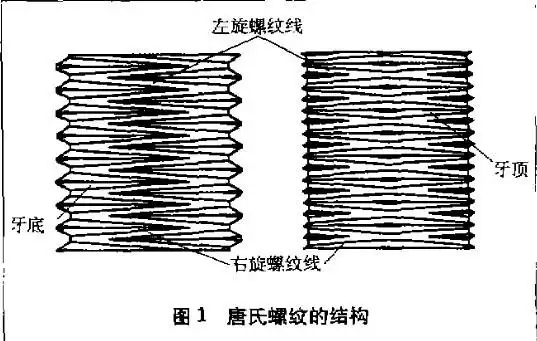
- MIL-N-45938:
- Pitch tolerance: ≤0.02mm
- Removal torque: ≤180% installation torque
- Used in San Francisco-Oakland Bay Bridge seismic joints
Engineering Selection Guide
(Decision tree graphic space)
Condition | Recommended Solution | Standard |
---|---|---|
>180°C thermal cycling | All-metal lock nut | ISO 2320 Grade A |
Saltwater exposure | Serrated flange (A4 stainless) | ISO 3506-1 |
Impact loads >10g | Spiralock® + cotter pin | NASM 1312-7 |
FDA environments | PTFE-coated Prevailing Torque | FDA 21 CFR 177.1550 |
Industry-Specific Applications
Aerospace (AS9100):
- Cockpit controls: DIN 980 all-metal nuts
- Engine mounts: Spiralock® + NASM 1312 testing
Wind Energy (IEC 61400):
- Tower flanges: HV serrated washers per DIN 6797
- Blade bearings: Castle nuts + LPU-coated pins
High-Speed Rail (EN 50126):
- Track fasteners: Double nut + Loctite 2701™
- Pantograph joints: Belleville stacks per DIN 6796
Avoid These Costly Mistakes
- Reusing deformed lock nuts (ISO 2320 prohibits >5 installations)
- Mixing stainless bolts with carbon steel washers (Galvanic corrosion)
- Overtorquing nylon inserts (>30% beyond spec melts nylon)
- Ignoring DIN 267-27 torque tolerance rules (±15% for critical joints)
Future Trends (2025+)
- Smart Fasteners: IoT-enabled bolts with embedded strain sensors
- Self-healing polymers: DARPA-funded nano-capsule thread coatings
- Additive manufacturing: Topology-optimized lock nut geometries
Conclusion: Lock It Right
Choosing anti-loosening fasteners isn’t guesswork—it’s physics-driven engineering. Whether you’re securing a satellite or a bicycle, match the solution to your vibration profile, environment, and industry standards. When in doubt, apply the golden rule: Two independent locking methods for critical joints.