When corrosion strikes a critical bolted connection, the results range from costly maintenance to catastrophic failure. The invisible battle against environmental degradation begins at the surface—specifically, with the protective coating you choose for your fasteners. In industrial applications, up to 30% of fastener failures trace back to inadequate corrosion protection, with repair costs often exceeding initial installation expenses by 500% or more 3. This guide demystifies the science behind zinc, nickel, and stainless steel coatings to help engineers and designers specify the optimal defense for their mechanical joints.
1 The Hidden Science of Corrosion: How Coatings Protect Fasteners
All metallic coatings function as either barrier layers (physically isolating the substrate) or sacrificial anodes (corroding preferentially to protect the base metal). Zinc-based coatings typically offer sacrificial protection, while nickel and stainless steel excel as barrier layers. When dissimilar metals contact each other in conductive environments (like salt spray), galvanic corrosion accelerates degradation—a critical consideration when pairing fasteners with base materials like aluminum or carbon steel 12.
Hydrogen embrittlement (HE) remains a silent assassin in high-strength fasteners (≥38 HRC). Electroplating processes can introduce hydrogen atoms into the metal matrix, leading to delayed brittle fracture under tension. This makes coating selection a safety-critical decision for applications like aerospace, automotive, or structural engineering 36.
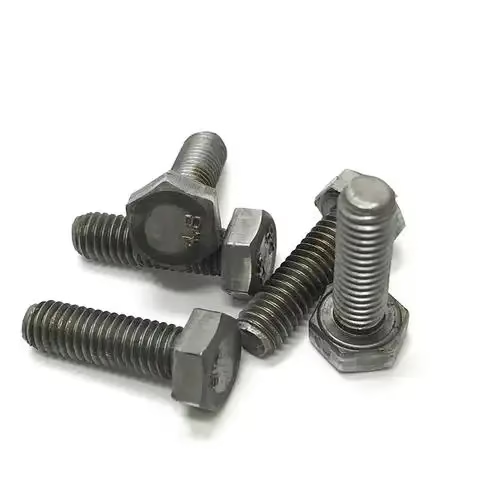
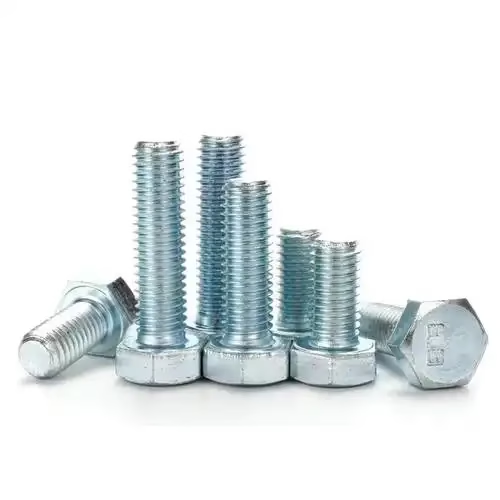
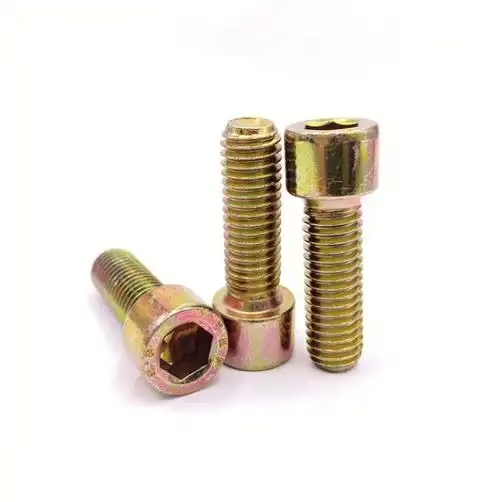
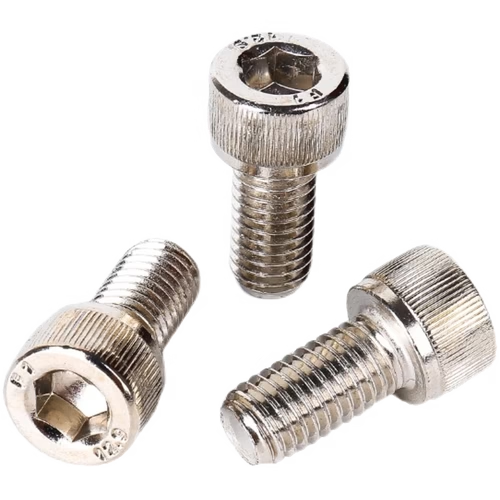
2 Zinc-Based Coatings: The Economical Workhorse
2.1 Electroplated Zinc
- Corrosion Resistance: 100-200 hours to white rust in salt spray testing (ASTM B117), suitable for mild indoor environments (ASTM Condition 1) 3
- Hydrogen Risk: High—requires baking within 1 hour post-plating for fasteners >38 HRC
- Cost: $0.05-$0.20 per fastener (lowest initial cost)
- Best For: Non-critical indoor assemblies with humidity control
2.2 Zinc-Nickel Alloy (10-20% Ni)
- Performance: 500-1,200+ salt spray hours—5-10x improvement over pure zinc 14
- Mechanism: Nickel refines coating microstructure, reducing corrosion current density (measured at 6.56 μA/cm² vs. zinc’s 10.66 μA/cm²) 1
- Hydrogen Management: Lower risk than zinc plating but still requires post-plate baking
- Applications: Automotive underbodies, marine equipment, and electrical enclosures
2.3 Non-Electrolytic Zinc Flake (e.g., Geomet, Dacromet)
- Technology: Water-based suspension of Zn/Al flakes baked at 300°C 1
- Advantages:
- No hydrogen embrittlement risk (no acid cleaning or electrolysis)
- Uniform coverage on complex geometries (thread roots, blind holes)
- Excellent heat resistance (up to 300°C)
- Limitations: Not recommended for fasteners <M8 or with internal drives due to buildup risks 3
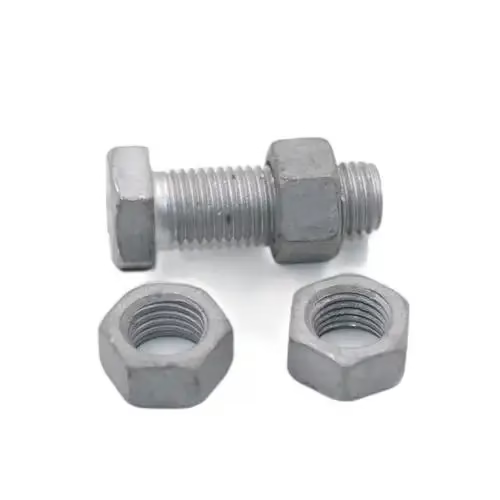
3 Nickel-Based Coatings: High-End Defense
3.1 Electroless Nickel (ENP)
- Barrier Properties: Amorphous phosphorus-rich layer blocks oxygen diffusion
- Thickness: Typically 25-75 μm—thicker deposits increase corrosion resistance
- Limitations: Brittle nature risks microcracking in threaded components
3.2 Nickel-Cobalt Alloy (ASTM B994)
- Breakthrough: Cobalt additions (≈33%) enhance hardness (up to 40 HRC) and corrosion resistance
- Uniformity: Electroplating ensures complete thread coverage—critical for nut/bolt pairs 68
- Hydrogen Barrier: Blocks hydrogen ingress, eliminating embrittlement failures
- Performance Guarantee: Leading manufacturers offer 5-year no-seize warranties and 20+ year service life predictions 8
3.3 Electrodeposited Zinc-Nickel
- Hybrid Approach: Combines sacrificial zinc with nickel’s barrier effect
- Marine Performance: Outperformed pure zinc by 300% in coastal exposure trials 5
4 Stainless Steel Fasteners: Beyond Coatings
While not a coating, stainless competes directly in corrosive environments:
Grade | Corrosion Resistance | Strength | Cost Index | Best Applications |
---|---|---|---|---|
304 | Moderate (no salt) | 70 ksi | 2.5x | Food processing, indoor |
316 | High (marine) | 75 ksi | 3.8x | Boats, chemical plants |
410 | Moderate (heat resistant) | 120 ksi | 3.0x | High-temp engines |
Caution: Stainless fasteners in contact with carbon steel can create aggressive galvanic pairs—insulation or coatings remain essential 5.
5 Coating Performance Face-Off: Data-Driven Comparisons
Recent testing exposed coated fasteners to simulated marine environments:
- Composite coatings (epoxy over Zn-Ni)
- Zinc-aluminum flakes
- Powdered zinc diffusion ≈ Hot-dip galvanizing
- Electroplated zinc
- Oxidation films (lowest performance) 5
Salt Spray Endurance Ranking:
text
Nickel-Cobalt > Zinc-Nickel ≈ Zinc-Al Flake > Hot-Dip Galvanized > Electroplated Zinc
Critical Finding: Zinc-aluminum coatings showed 9.50–10.66 μA/cm² galvanic current density when coupled with steel—higher than zinc-nickel’s 6.56–8.15 μA/cm², confirming nickel’s superior performance in mixed-metal joints 1.
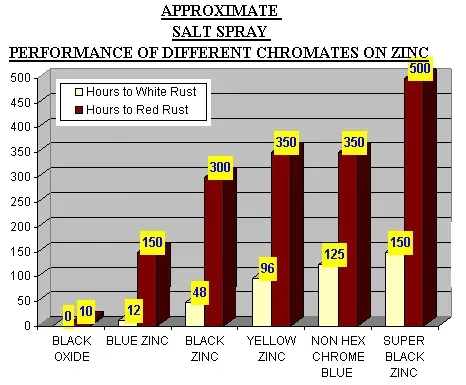
6 The Ultimate Selection Framework
Follow this decision tree to eliminate coating guesswork:
- Assess Environmental Severity
- Mild (indoor): Electroplated zinc
- Moderate (occasional condensation): Zinc flake
- Severe (salt exposure): Zinc-nickel or nickel-cobalt 3
- Check Strength Requirements
- 1,200 MPa tensile strength: Avoid electroplating or specify strict baking protocols
- Validate Functional Needs
- Thread engagement: Avoid mechanical plating on threaded parts 3
- Dimensional tolerances: Thin coatings (<8μm) preferred for precision threads
- Account for Hidden Costs
- Zinc-nickel’s higher initial cost often offsets 3-5x lifetime extension in corrosive service
7 Future-Proofing Fastener Technology
Emerging coatings leverage elemental synergies:
- W-Cu-Ni-Sn additions refine rust particles into protective layers, extending recoating intervals by 2.4x 7
- Tin-modified steels accelerate anodic reactions at defects, slowing underfilm corrosion
- 100% traceability systems now pair coatings with digital IDs for predictive maintenance
Final Verdict: While zinc coatings dominate cost-sensitive applications, nickel-cobalt alloys represent the new frontier for critical joints in harsh environments. For coastal or chemical exposure, ASTM B994 nickel-cobalt delivers unmatched corrosion resistance and hydrogen resistance—making it the “smart bolt” solution for zero-failure systems.